Rubber Compounding
Rubber compounding is the process of mixing raw rubber materials, such as natural rubber or synthetic rubber, with various additives and chemicals to achieve desired properties and characteristics. These additives can include fillers, plasticizers, accelerators, antioxidants, and curing agents. The compounding process is crucial in determining the final properties of the rubber, such as hardness, elasticity, and resistance to chemicals or temperature. It is typically done using specialized machinery, such as a two-roll mill or internal mixer, to mix and blend the ingredients evenly before shaping and curing the rubber into its final product.
Rubber technology involves the study and development of materials made from natural or synthetic rubber. This field covers the formulation, processing, and applications of rubber products in various industries, such as automotive, construction, healthcare, and consumer goods. Rubber technology also includes research on improving the performance, durability, and sustainability of rubber materials through innovations in material science, engineering, and manufacturing processes. Key areas of focus in rubber technology include rubber compounding, vulcanization, rubber processing techniques, product design, testing, and quality control.
Rubber Technologist with more than 30 years of experience, having developed more than 300 compounds.
Total Installed Capacity of 5,000 Tons p.a. including
- 2 Banberry Intermix
- 2 Kneaders
- 3 Auto Weighing Systems with Bar-coding
- 2 Compound Testing Labs
Line-1: 35 Ltr Inter mixer with Two Roll Mill capacity of 16 * 42” along with Batch of Machine Cooling System
Line-2: 35 Ltr Kneader with Two Roll Mill capacity of 16 * 42”
16 * 42 “inch Two Roll Mill with Stock Blender for Color Compound mixing
Precision Pre-former (Bare well Slug) with 250mm (about 9.84 in) Diameter
Computerized Weighing setup with Full Proof System


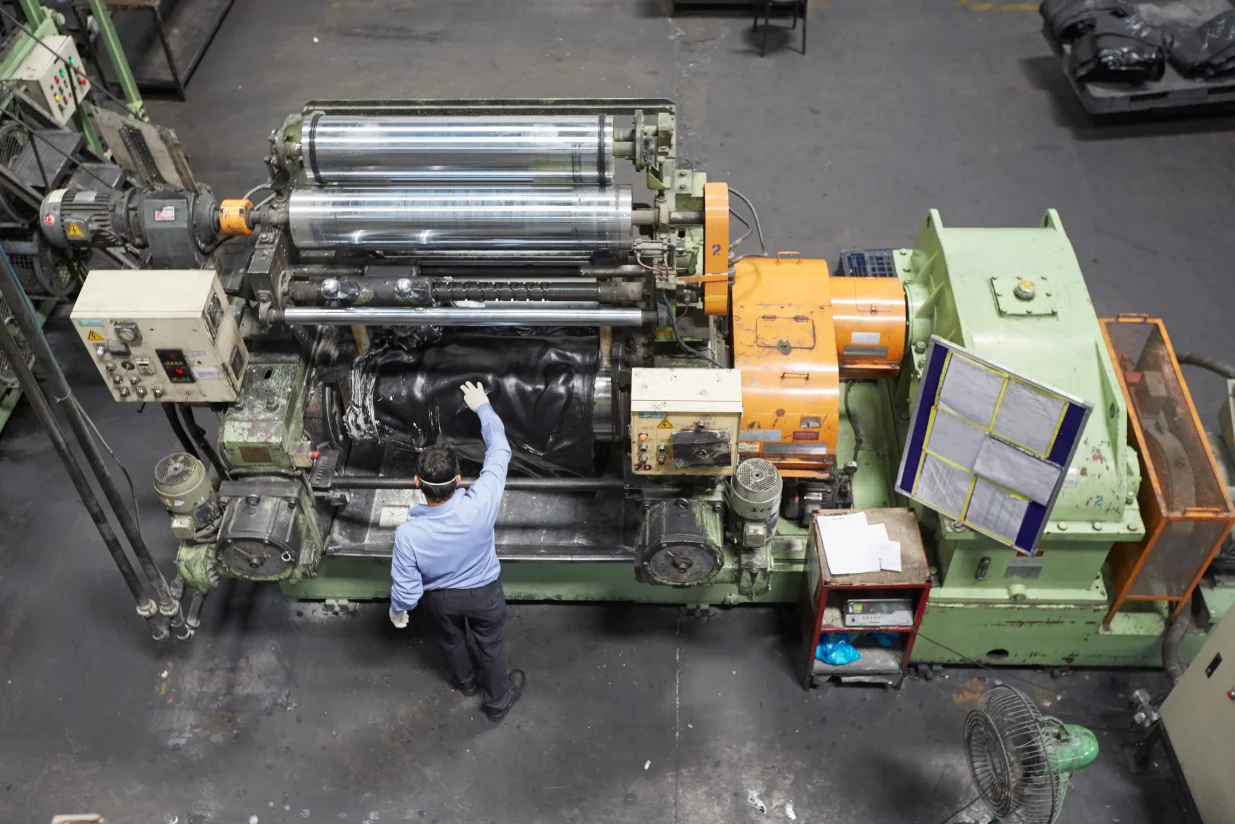